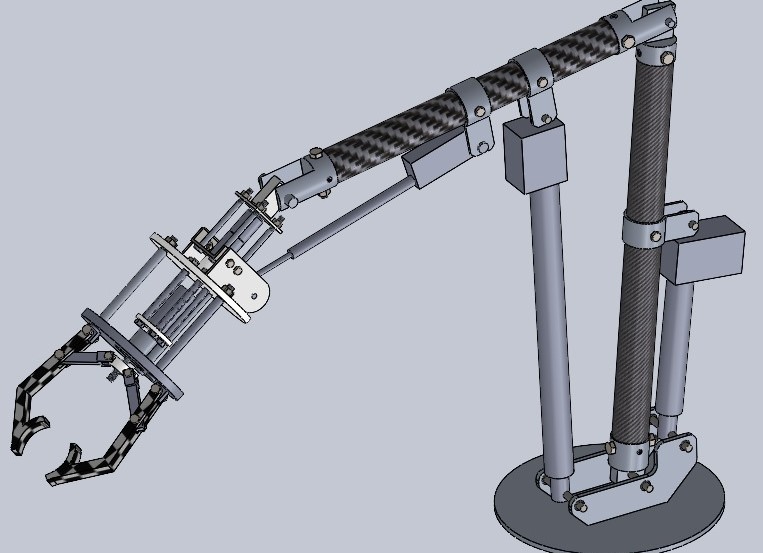
Robotic Arm
We design and build a multiple degree-of-freedom robotic arm that should be capable of performing the following tasks: Lift/drop objects upto 5 kgs, Turn knobs, Push buttons, Open drawers , and other precise movements…There is a variety of stuff we work towards in this subsystem: mechanisms, materials, easier and precise control, robustness